Additive manufacturing aboard a moving vessel at sea using passively stabilized stereolithography (SLA) 3D printing
Document Type
Article
Date of Original Version
1-1-2020
Abstract
In this paper we investigate the use of passive stabilization to support stereolithography (SLA) printing aboard a moving vessel at sea. 3D printing is a useful technology onboard a seagoing vessel to support engineering development, shipboard maintenance, and other applications when land-based manufacturing resources are unavailable. SLA printed material is particularly suited for underwater applications requiring sealed housings, since SLA printers are capable of producing high-resolution models that are fully solid and impervious to water. Hydrostatic pressure can quickly compromise parts created using standard fused filament fabrication (FFF) 3D printing. However, the dynamic environment onboard a moving vessel could impact the ability of an SLA printer to selectively cure voxels in a liquid resin bath as it undergoes constant motion, and can cause spilling over the walls of the resin tank. Using passive stabilization platforms onboard moving research vessels, we successfully printed a number of parts with no discernable differences from those produced in a traditional land-based laboratory. As a practical demonstration of this capability, we printed at sea underwater pressure housings that remained sealed to 200 m water depth with functional integrated internal electronics. No post-print machining was required to create the sealed housings. This work lays the foundation for lithographic 3D printing in seagoing oceanographic and naval applications, and additionally presents an economical approach for producing custom waterproof pressure housings in the field.
Publication Title, e.g., Journal
Additive Manufacturing
Volume
31
Citation/Publisher Attribution
Phillips, Brennan T., Josh Allder, Grady Bolan, R. S. Nagle, Allison Redington, Tess Hellebrekers, John Borden, Nikolai Pawlenko, and Stephen Licht. "Additive manufacturing aboard a moving vessel at sea using passively stabilized stereolithography (SLA) 3D printing." Additive Manufacturing 31, (2020). doi: 10.1016/j.addma.2019.100969.
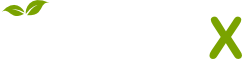
- Citations
- Citation Indexes: 36
- Patent Family Citations: 1
- Policy Citations: 1
- Usage
- Abstract Views: 16
- Captures
- Readers: 116